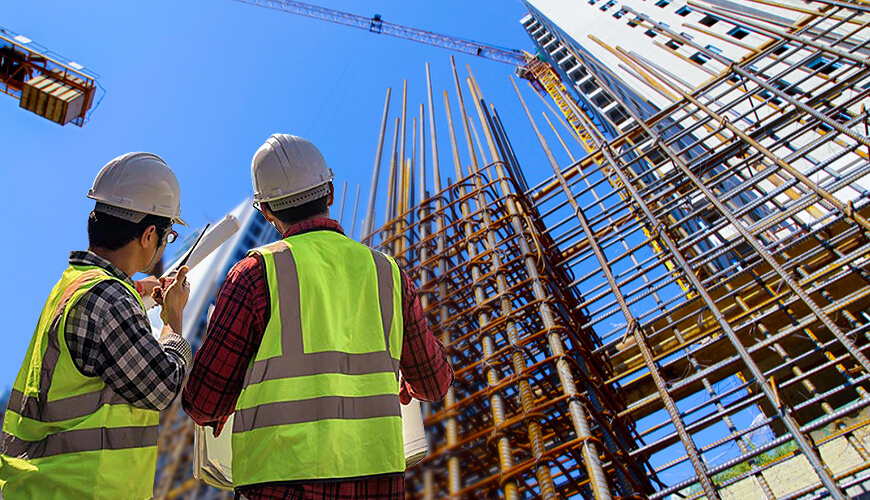
Rebar Detailing Process – Steps Toward Sustainable Steel-Concrete Structures
Rebar Detailing Process – Steps Toward Sustainable Steel-Concrete Structures
In the AEC Industry, Rebar Detailing is less- known or ignored profession. Yet, as a process, it remains vital and significant in providing strength to the structure. Rebar detailing services brings structural integrity by providing buildings resistance to collapses. The accuracy in rebar fabrication, estimation, rebar connections, rebar detailing, and rebar placing develops a durable and sustainable structure.
Fabrication drawings of the detailing process specify the quantity of rebar required, description, placement, dimensions of bending shapes, and laps related to rebar. Rebar estimation helps in predicting the material and number of quantity, to build the structure. And placing drawings acts as a guide, leading to a productive construction of reinforced concrete structures.
Rebar detailing has a broader scope and gets used for residential projects, commercial, bridges, highways, parking, stadiums, and other structural ventures. 3D rebar detailing and the use of advanced software like Tekla makes the rebar detailing process effective and efficient.
What Is Rebar Detailing?
Rebar detailing is done based on the structural engineer’s drawings. These drawings determine the rebar quantity required in each part of the structure, i.e., right from the footing to other parts of the structure. It makes the structure sustainable and durable. Rebar’s size, spacing, zoning, layering of bars, etc., gets revealed by the information in the drawings.
The rebar detailer is responsible for interpreting the drawings created by the structural engineer. And then develop new drawings, rebar shop drawings that can get comprehended by the rebar placer. Shop drawings should be practical, giving clear information about the fabricated steel for getting assembled at the site.
Rebar detailing creates rebar placing drawings, guiding the workmen or rod men placing the bars before concrete gets poured. The detailing process generates an accurate bar-bending schedule. It is for smooth placement and fitting of fabricated bars in the concrete with a detailed reinforcement requirement. The bar schedule is also used for accounting and invoicing.
The rebar detailing drawings are verified and approved by the structural engineer to cross-check if rebar shop drawings and rebar schedule comply with the structural design intent and minimizes the communication gap. Besides, rebar wastage analytics helps in reducing the present potential scrap in rebar drawings.
The use of BIM and customized tools for rebar detailing automates several rebar detailing and documentation tasks. The information for the rebar fabrication process, such as rebar length, sizes, and bends, should meet the standards like CRSI and ACI. Access to the architectural model in Revit brings advanced coordination, and design changes are visible in real-time. An information-rich and detailed rebar design achieved with 3D technology.
Extensive Rebar Detailing Process
The rebar detailing process follows the design codes and standards that vary with the project location. The building codes specify the size and location of each rebar in the drawings. Further, data such as anchorage length, mechanical connections with reinforced concrete, etc., are mentioned. Since different grades of steel get used in structural projects, it is vital to add steel grades in the rebar detailing process.
Steps of the Rebar Detailing Process
1. Interpretation of Structural Drawings
The structural drawings and specifications developed by structural engineers later get interpreted by the steel detailers. So it needs an understanding of civil and structural drawing, including clarity on how steel is transported, fabricated, and erected. An accurate interpretation results in a more feasible drawing and detailing of the rebar and concrete.
2. Development of Bar-bending schedules
After interpreting the structural drawings, the detailer develops a bar bending schedule. The comprehensive list of the bar-bending schedule includes
- Bar Number
- Bar shape
- Diameter
- Spacing
- Length of bar
- Cutting length
- Number of bars
The bars get grouped for the structural units in the form of a beam, column, etc. For buildings, bars get listed floor-wise. And they are listed in numerical order in the schedule. Separate sheets get used to generate the bar bending and cutting schedules.
The detailers, fabricators, contractors, steel fixers, and quantity surveyors use the bar-schedule.
3. Compliance with Design standard and codes
The bends, hooks, loops, concrete cover, spacing, tie points of reinforcement bars, etc., needs to follow design codes and standards to strengthen the structure.
The guidelines detailing the reinforcement in concrete structure for construction as per the standards EC2 (Euro code 2) and ACI (American Concrete Institute) are as follows.
Mandrel diameters for bent bars as per EC2 standard
Minimum Mandrel diameter is the smallest diameter at which no bending cracks appear. It ensures the integrity of concrete inside the bar.
For bars and wires with a diameter more or equal to 16 mm, the required minimum mandrel diameter for bends, hooks, and loops is 4 ᴓ. And for bars and wires of less than 16 mm diameter, the minimum mandrel diameter is 7 ᴓ.
Standard bends, hooks, and loops as per EC2 standard
EC2 specifies a standard equivalent anchorage length and anchorage method for rebar bends, hooks, and loops. Specific shapes for ties and stirrups need to be maintained according to the EC2 standard.
Bar Spacing
As per ASI and EC2, bars should get spaced so that, concrete when poured, results in satisfactory bonding and strength development. ACI1318 Code followed for the minimum spacing of bar.
The horizontal and vertical distance between individual parallel or horizontal bars should not be less than larger of d9+5mm (d9 is the maximum aggregate size) and 20mm.
EC2 and ASI also lay out the guidelines for concrete cover requirements, bundled bars, etc.
4. Development of Rebar placement drawings
Placing drawings are the detailed drawings instructing the ironworkers where to place the reinforcing bars within the formwork. The drawings include details such as:
- Concrete cover
- Bar spacing
- Bar support layout
- Tolerance on reinforcement position
The concrete cover lies on top of the surface of the reinforcement closest and is the nearest concrete surface. Reinforcing gets located at a minimum distance from the surface of the concrete. And it provides a protective layer of concrete cover. The protection is against the environment, like fire and corrosion. The required minimum concrete cover as per EC2 standard is 15 mm.
ACI 315 detailing standard states the responsibility for preparation, review, and approval of placing drawings. For preparing the drawings, the detailer is responsible for performing all instructions on the contract documents.
5. Approval of drawings
The bar bending schedule and placing drawings should get finally approved by the architect and engineer. It reduces the chances of misinterpretation of structural drawings by the detailer and boosts error-free construction. An architect and engineer who know the potential areas of reinforcing steel at all points, and performed the analysis of loading effects on the structure, is therefore aware of the structural specifications. Thus, the architect/engineer is the right person to seal the drawings.
Expertise Required for Rebar Detailing
Rebar detailing has a significant role in developing the structural strength and determining the durability of a building. It requires extensive involvement and meticulous care for rebar detailing and related services.
Companies involved in rebar detailing services require a team with an understanding of structural and civil disciple. The team is to gather information from the project specification. It is imperative to get the structural design intent. How a structure is created using footings, slabs, beams, etc., gives a hand in rebar detailing. The architectural, MEP, and construction drawings from other disciplines require to get interpreted for a consistent, clash-free, and unambiguous rebar detailing. Notes and schedules related to rebar detailing should be read and considered in the detailing process. If any information is missing, and there is a state of confusion and conflicts, RFI should get raised for clarity.
A basic understanding of the structural elements is required to get a precise detailing of the rebar. As for the beam, details such as its dimensions, bar supports, concrete cover (on top, bottom, and side of a beam), lap length, various rebar in a continuous beam, etc., are needed.
Detailers require to have a comprehensive knowledge of rebar detailing codes and guidelines. It will help choose the code, bend shapes and pin diameter suggested in the code, lap lengths, calculate development & cut lengths, standard hook lengths, calculate bar sizes, etc.
Clarity of fabrication process support in deciding whether to use CNC machines or not, knowledge on rebar cutting and bending, selecting the format of bar bending schedule, the maximum length of the bar for shipping, and truckload for rebar shipping.
Rebar placing drawing and its presentation style should meet the expectation of the client. Companies must follow 2D and 3D detailing software approach to offer an error-free, accurate, and cost-effective rebar detailing process and drawings.
Rebar Detailing Is a Specialist’s Job – Let the Experts Handle It
OneStop AEC (OSA) is one of the best Structural engineering service providers with expertise in rebar detailing, fabrication, rebar estimation, and rebar placing services. At OSA, leverage other crucial structural engineering services, like Tekla steel detailing, structural design and drafting, and shop drawing with our team of experts. We evaluate our client’s requirements thoroughly and provide the required rebar services to plan and develop a sustainable structure. Get in touch with OSA for a strong, durable, and sustainable reinforced concrete structure and handle several construction challenges of your project.
0 comments
Write a comment